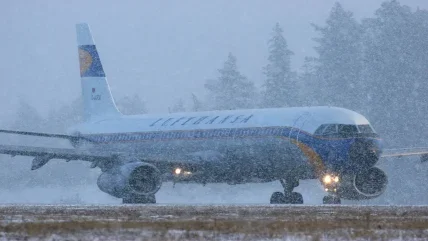
Whether it’s icing or low runway friction, winter conditions are a serious threat to aircraft. To meet the subzero challenge, airports require a combination of expert ground staff, the latest equipment, and the most efficient snow-clearing and de-icing techniques.
Stockholm Arlanda is one of the world’s best at handling winter. Since it opened in 1962, it hasn’t closed once due to adverse conditions, despite its northern location and exposure to heavy ‘lake-effect’ snowfalls (when freezing air from the north-east meets moist maritime weather from the Baltic Sea).
“Arlanda takes great pride in its track record but never forgets its safety target,” says Christian Nyberg, air and landside maintenance manager. “Most of all, it has to measure and report the actual conditions at the airport to ensure that all operators have all the necessary data to perform safe operations.”
Between the aprons, aircraft parking areas and three runways, Arlanda has to clear snow from more than 250,000m2 of tarmac. With so much work to do throughout the winter, airport operator Swedavia invests heavily in staff training and the very best snow-clearing vehicles.
All together now
When ploughing the runways, up to ten plough-sweeper-blowers (PSBs) run together in precise formation. Each machine shoves snow to the vehicle behind it and, ultimately, off the edge of the tarmac. They can sweep the 3.3km main runway in about ten minutes, giving them a fair claim to be the world’s fastest.
The sweeping teams use pre-planned routes, clearing each one at intervals of 35–60 minutes. Different routes are used, depending on weather and traffic, with the priorities being the runway in operation, and its taxiways and emergency routes, plus the required aprons and parking stands. The air traffic control tower uses radio to direct the sweeping-team supervisors.
“The drivers follow their manoeuvres precisely, so air controllers, who also know the routines, can time arriving and departing flights down to the minute,” explains Nyberg.
Arlanda has 100 or so different vehicles just for snow clearing. On the runways and taxiways, the PSBs go first, followed by an anti-skid spreader, snowblowers and friction-test cars.
“Since the airport is expanding, traffic volumes are increasing, aircraft are getting bigger and new snowremoval vehicles must have every available improvement,” says Nyberg. “Arlanda is striving to be at the front at all times.”
In line with this ambition, Swedavia has ordered 30 new ploughs. More than 17m long and weighing nearly 30t, these double-engined behemoths raise the maximum sweeping speed to 40km/h.
With ten PSBs sucking down 400L of fuel between them every hour, reducing emissions is another priority.
Swedavia wants to eliminate fossil carbon dioxide from its own operations by 2020; Arlanda’s vehicle fleet is already largely made up of electric or hybrid biodiesel vehicles. Running the new PSBs on a mix of biogas and diesel has already reduced their emissions by 70%; introducing renewable diesel will cut this to zero. Standardising the vehicle fleet also makes for lower maintenance costs.
“Arlanda is continually pushing producers of heavy machines to invent bigger, better and ‘greener’ vehicles,” says Nyberg. “Swedish airports were the first in the world to use biogas-powered machines for snow-clearing.”
Each metre of snow left by the PSBs weighs about 120kg. To cope, the snowblowers can move up to 8,000t every hour, blowing it 50m off the runway while driving at 30km/h.
Next, the de-icing spreader drops a 24m-wide strip of anti-skid agent on the runway; a spreader with a width of over 40m is being tested, too. Arlanda uses potassium formate, an organic salt that quickly clears any remaining snow but also decomposes naturally.
“It is expensive, but friendlier to the environment than most other chemical anti-skid agents on the market,” says Nyberg, noting that all meltwater is collected and treated. “The ideal is good friction values with as little contamination as possible.”
On the skids
With snow removal complete, staff test the runway friction and the airport passes this information to pilots. Each pilot then decides whether the friction is sufficient to land safely. The friction value also determines how often a runway must be ploughed and treated with anti-skid agent.
Orchestrating these critical operations demands clear communication and collaboration between Arlanda’s lead snow coordinator and all other airport functions. The forecast is checked twice daily and any potential disruption triggers a tactical traffic forum meeting.
These involve the airport duty officer and snow coordinator; the control tower’s watch supervisor; traffic planning; weather forecasters; and ground handling companies.
“All companies and organisations at the airport contribute to keeping the airport operational,” says Nyberg. “In heavy snowfall, it is especially important that everyone helps out in order to achieve as high a capacity as possible.”
Before, during and after the winter, the airport’s managers meet fortnightly with the snow removal team supervisors to review working practices and to ensure each group’s routines synchronise correctly. When the snow and ice are gone, it’s time for a more thorough review.
“Planning is part of Arlanda’s year-round business but is intensified during the summer months to get well prepared for the winter,” explains Nyberg.
“There are meetings with the handling companies as well as with the biggest airlines and the air traffic control centre.”
“Parts that have worked well during the winter are worked through, as well as those that haven’t performed quite so effectively,” he continues. “Usually, these meetings end up with 50–70 actions for improvement.”
To provide 24/7 snow clearance cover, five teams of up to 30 people work 12-hour shifts between October and April. The airport takes on an extra 75 workers in winter, nearly trebling its field maintenance team’s headcount from 35 to 110.
Each September, new seasonal staff take a three-week induction course at the airport’s in-house academy. Returning workers have their own training plan that updates them on any changes to work routines or airport operations since their last employment.
“Finding the right competence needed to carry out the different kind of jobs in our winter operations is crucial,” says Nyberg. “Employees need to be excellent in handling machines, be good at handling stressful situations, communicate clearly, be good team players and have high safety awareness.”
Fluid dynamics
De-icing aircraft before take-off is the other vital winter task. Equipment and application techniques have evolved significantly over the past decade to make it more effective and efficient.
Truck-based glycol blenders are a good example of this progress. These increase an airport’s overall liquid capacity and let workers quickly reblend fluids in the truck to meet new freeze-point requirements as weather conditions change.
“One of the latest initiatives is to manufacture de-icing fluids in the vehicle itself by blending freezing-point depressant with the additive package and the glycol,” says Jacques Leroux, chairman of the SAE G-12 ground de-icing committee.
“This is being tested at Chicago Airport at the moment.”
Minimising the amount of liquids used is another priority, with vehicle-based automatic metering showing crews exactly how much has been applied. Recycling used fluid is also getting more attention.
“I know that there are ongoing discussions about glycol recovery,” says Per Lindgren, ground operations manager at Arlanda.
Applying type-1 followed by type-4 de-icing fluid is a further advance that is now standard procedure in North America. This prevents residues forming that can affect an aircraft’s flight characteristics.
The biggest change afoot, however, is the global move towards common de-icing facilities (CDFs). Along with that goes the need for standard de-icing processes, rather than staff implementing each airline’s individual routines.
“If you try to have five, ten or 80 different procedures at a single facility, it becomes very difficult, or even impossible,” says Leroux. “You can have errors because the people doing the de-icing have too much to remember, and that leads to confusion.”
As well as increasing safety, standardised de-icing processes boost efficiency and so reduce costs, particularly for training. Where common standards are already used across airports and regions, as in Canada, staff can easily transfer from one location to another without retraining. Leroux has worked with leading industry bodies like the FAA, EASA, AEA and ICAO to agree a new set of common global standards. Running since 2007, this project is now coming to fruition with a final set of documents agreed and regional authorities changing their rules to reflect them.
At Arlanda, de-icing is carried out by ground handling companies working directly for each airline, with the airport providing holding areas for the work. However, CDFs are currently under consideration.
“Stockholm Arlanda has made a report on the feasibility and cost of building a central de-icing location,” says Lindgren. “Building would be very costly and it’s questionable that the cost can be justified.”
Whether it’s de-icing, or any other aspect of winter operations, the airport constantly looks for new ways to improve. Its managers regularly meet with colleagues from other European locations – and receive plenty of visitors eager to learn from Stockholm’s vast experience.
With its sharp focus on winter excellence, Arlanda’s 55-year run of uninterrupted operations doesn’t look like ending any time soon.